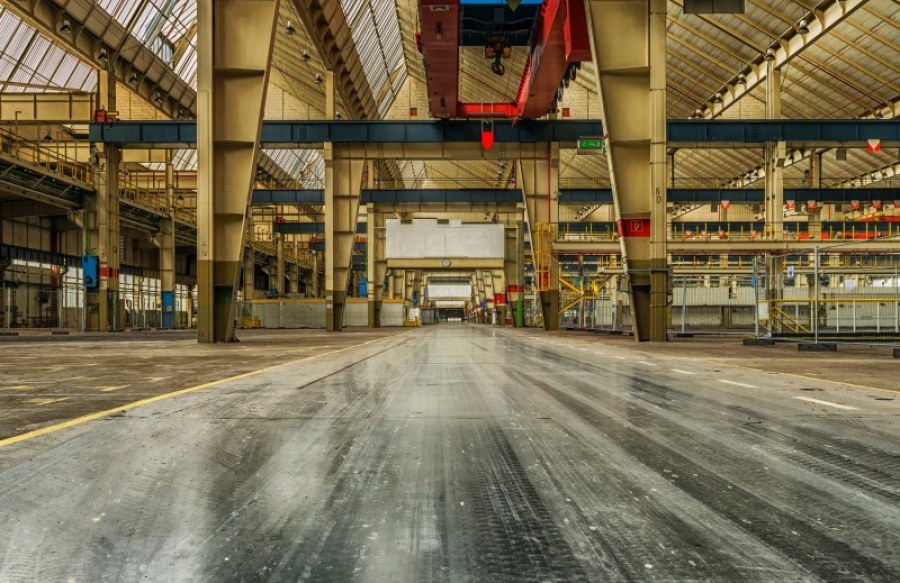
Z perspektywy przedstawionych powyżej wyzwań prawdziwym trendem wśród przedsiębiorstw produkcyjnych stały się projekty optymalizujące obsługę łańcucha dostaw, zaawansowane harmonogramowanie produkcji, obsługę stanów magazynowych z poprawą ich rotacji, aktywności pozwalające zminimalizować produkcję w toku oraz bardzo precyzyjnie zaplanowane inwestycje zapewniające bezproblemową produkcję. W zależności od aktualnego stanu oprogramowania używanego przez przedsiębiorstwo albo były to projekty powiązane z upgrade’m lub wdrożeniem całej nowej wersji DSR 4FACTORY, albo chirurgicznie precyzyjne wdrożenia konkretnego modułu. Zainteresowanie tego typu projektami nie słabnie i w 2022r na pewno wśród najczęściej realizowanych będą: wdrożenie narzędzi do harmonogramowania produkcji APS 4FACTORY (na bazie Siemens Opcenter APS), lepsze zarządzanie przestrzenią magazynową WMS 4FACTORY (na bazie QAD Warehousing), zminimalizowanie awaryjności parku maszynowego przez poprawę procesów utrzymania ruchu EAM 4FACTORY, przyspieszeniu przepływu informacji o postępie produkcji i pojawiających się zakłóceniach poprzez rejestrowanie zdarzeń przez operatorów lub bezpośrednio z maszyn na hali produkcyjnej MES 4FACTORY. Dla firmy DSR ważne jest, że zainteresowanie tymi projektami jest równie duże wśród dotychczasowych klientów DSR, jak i nowych przedsiębiorstw produkcyjnych, które mogą wdrożyć rozwiązanie ERP 4FACTORY, albo też używać innego wcześniej wdrożonego ERP-a (DSR zapewnia integrację przez dedykowaną szynę danych ESB 4FACTORY działającą w trybie on-line).
Przeczytaj również: https://www.dsr.com.pl/wdrozenie-simatic-it-preactor/
Kontynuowanym trendem jest, że dla nowo otwieranych zakładów produkcyjnych międzynarodowych koncernów, jak i dla firm start-up’owych nie ma półśrodków i realizowane jest pełne wdrożenie systemu ERP 4FACTORY w chmurze (na bazie QAD Adaptive ERP) wzbogacone o uruchomione funkcje harmonogramowania produkcji APS 4FACTORY i dostęp do pozostałych wyspecjalizowanym narzędzi wspierających rewolucję przemysłową 4.0 z pakietu DSR 4FACTORY. Firmy chcą mieć wdrożony pełen pakiet skutecznych narzędzi od samego początku rozpoczynanej działalności biznesowej.
Warto też podkreślić, że począwszy od 2022 r. pakiet DSR 4FACTORY wzbogacony jest o dodatkowe narzędzie AI 4FACTORY, które zostało wytworzone w ramach projektu PMSA (Production Management Smart Advisor) współfinansowanego z Funduszy Europejskich „Inteligentny Rozwój”. AI 4FACTORY jest narzędziem inteligentnej rekomendacji zmian w procesach produkcyjnych w celu ich optymalizacji, wykorzystującym techniki kognitywne. Nowa metoda rekomendacji pozwala na szeroki udział pracowników w podejmowaniu decyzji dotyczących sposobu działania, pozwalającego na ciągłą optymalizację procesu produkcyjnego. Opracowane narzędzie z jednej strony umożliwia pracownikom produkcyjnym (w tym operatorom maszyn) podejmowanie decyzji związanych z ich obszarem działania, a z drugiej strony umożliwia kadrze kierowniczej na weryfikację adekwatności i skuteczności decyzji optymalizacyjnych. Istotnym elementem narzędzia jest możliwość prognozowania zatrzymań maszyn wraz ze wskazaniem czasu i prawdopodobieństwa ich wystąpienia. Pozwala to na prowadzenie działań prewencyjnych zapobiegających niepożądanym postojom maszyn. Rozwiązanie to, w pełni współpracując z człowiekiem, wpisuje się w koncepcję Przemysłu 5.0, w którym to człowiek i maszyna pracują w pełnej synergii. Rozwiązanie nastawione jest na zwiększenie efektywności w obszarach jakości produktu, wykorzystania parku maszynowego i tempa produkcji.
Przeczytaj również: https://www.dsr.com.pl/czym-charakteryzuje-sie-zaawansowany-i-elastyczny-system-produkcyjny/
Koncepcja produkcji just-in-time jest jednym z filarów Toyota Production System (TPS). System ten został zaadaptowany przez całą branżę automotive, mając kluczowy wpływ na kształt procesów bezpośrednio generujących wartość dodaną, ale też procesów pomocniczych, takich jak właśnie dostawy. Rezygnacja z realizacji dostaw w trybie just-in-time w przedsiębiorstwie z sektora automotive byłaby więc posunięciem kosztownym i niezrozumiałym dla partnerów biznesowych. Z uwagi na specyfikę produktów jakimi są samochody i ich podzespoły, odejście od koncepcji just-in-time w łańcuchu dostaw byłoby też w wielu przypadkach fizycznie niemożliwe. Nawet niedrogie miejskie auto może zostać skonfigurowane przez klienta na ponad pół miliona sposobów, a to oznacza ogromną różnorodność części dostarczanych na linie montażowe pojazdów.
Na etapie konfiguracji pojazdu klient może decydować o rodzaju wykończenia wnętrza, systemie info-rozrywki lub rodzaju klimatyzacji. Klient dostaje też do rąk długą listę opcji dodatkowych, z których może wybrać na przykład tempomat, sportowe zegary czy chłodzony schowek. Wszystkie te wybory przekładają się na budowę jednego elementu - modułu deski rozdzielczej, który dodatkowo występuje w wersjach z kierownicą po lewej lub prawej stronie. W praktyce ta część ma kilka tysięcy możliwych konfiguracji. Przy tak wysokiej liczbie konfiguracji i wielkości produkcji sięgającej tysiąca pojazdów dziennie, utrzymanie na magazynie odpowiedniej liczby części we wszystkich dostępnych wersjach, a następnie sprawne dostarczenie ich na obszar produkcyjny jest technicznie niewykonalne. Zamiast tego podzespoły takie jak: wspomniana deska rozdzielcza, kierownica czy fotele, dostarczane są bezpośrednio na linię montażową. Części oczekują w krótkich kolejkach zgodnie z sekwencją ich montażu. Podzespoły są parowane z nadwoziem już na etapie ich produkcji i często współdzielą numer VIN z nadwoziem. Jest to wysoce rozwinięta forma dostaw just-in-time wymagająca zaawansowanych narzędzi informatycznych, dopracowanych procesów produkcyjnych i doskonałych dostawców.
Przeczytaj również: https://www.dsr.com.pl/kluczowe-wskazniki-produkcyjne-wykorzystanie-mocy-produkcyjnych-i-przepustowosci/
Dostawy just-in-time mogą być jednak z sukcesem realizowane w innych sektorach, a korzyści jakie z nich płyną są uniwersalne. Niezależnie od branży, każda firma zyska przecież na odzyskaniu kapitału zamrożonego w zapasach, zredukowania kosztów utrzymania magazynów oraz ograniczenia marnotrawstwa związanego z oczekiwaniem na materiał lub zbędnym transportem.
Źródło:
0 komentarzy